丁基胶挤出机的生产流程是以**原料预处理—塑化挤出—成型—后处理**为核心的连续化工艺,需严格控制温度、压力、速度等参数以确保产品质量。以下是其详细生产流程及关键控制点:
生产前准备**
原料预处理**
• **丁基胶原料**:颗粒或块状丁基橡胶需预先干燥(60-80℃烘烤2-4小时),去除水分(含水率<0.1%)。
• **添加剂混合**:按配方加入填料(炭黑、碳酸钙)、增塑剂、抗氧剂等,通过密炼机或高速搅拌机混合均匀。
• **过滤除杂**:通过滤网(目数40-80目)去除杂质,丁基胶挤出机价格_丁基胶挤出机价格防止堵塞螺杆或口模。
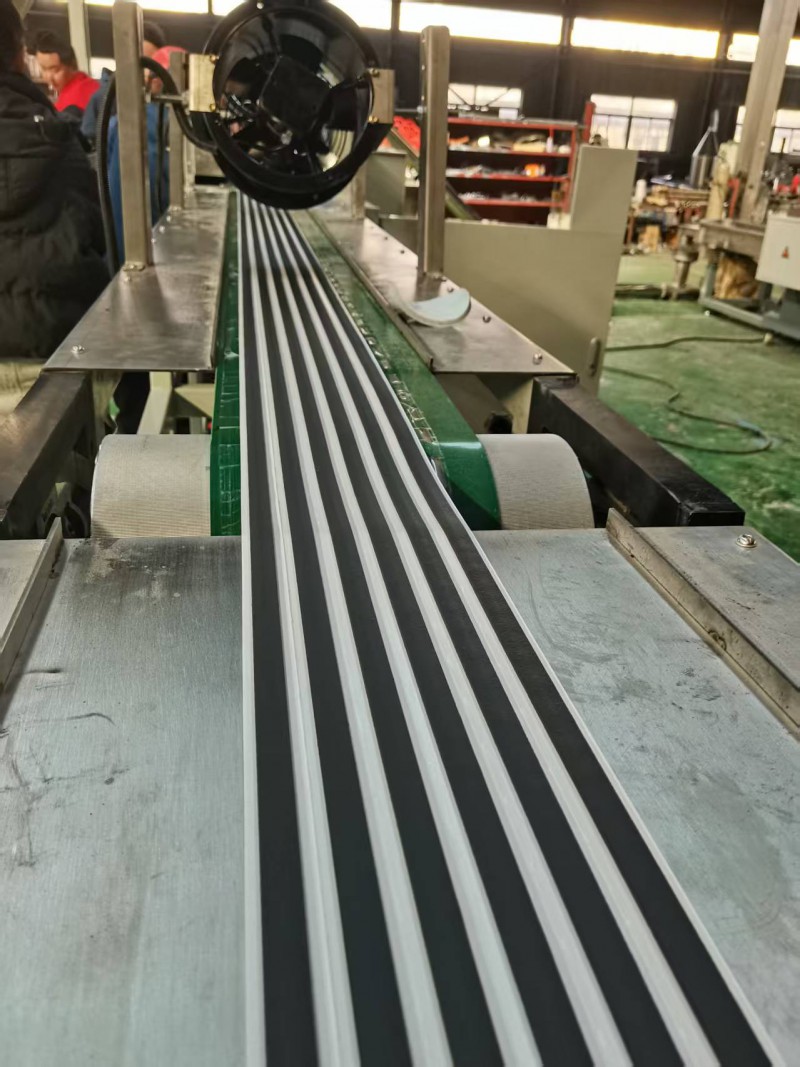
设备调试**
• **温度设定**:分阶段预热机筒(进料段150℃→压缩段170℃→均化段190℃→口模200℃)。
• **模具安装**:根据产品形状(胶条、胶管等)安装对应口模,校准同心度与间隙。
• **参数预设**:设定螺杆转速(20-60 rpm)、喂料速度、牵引速度(与挤出速度匹配)。
挤出成型流程**
喂料与塑化**
• **喂料段**:原料通过料斗进入螺杆进料区,螺杆旋转推动原料向压缩段移动。
• **压缩段**:螺杆螺槽深度逐渐变浅,原料被压缩并受剪切力作用升温塑化。
• **均化段**:熔融丁基胶进一步均质化,温度、压力稳定后进入口模。
挤出成型**
• **口模成型**:熔融胶料通过口模定型丁基胶挤出机价格_丁基胶挤出机价格,形成连续产品(如胶条、胶管)。
• **关键控制点**:
◦ **压力控制**:机头压力需稳定在15-30 MPa(过低导致缺料,过高易胀模)。
◦ **温度波动**:口模温度误差≤±2℃,防止表面粗糙或气泡产生。
冷却定型**
• **水冷或风冷**:产品离开口模后进入冷却槽(水温10-25℃),快速降温定型。
• **真空定径**:用于管材生产,通过真空吸附确保尺寸精度(如直径误差±0.2 mm)。
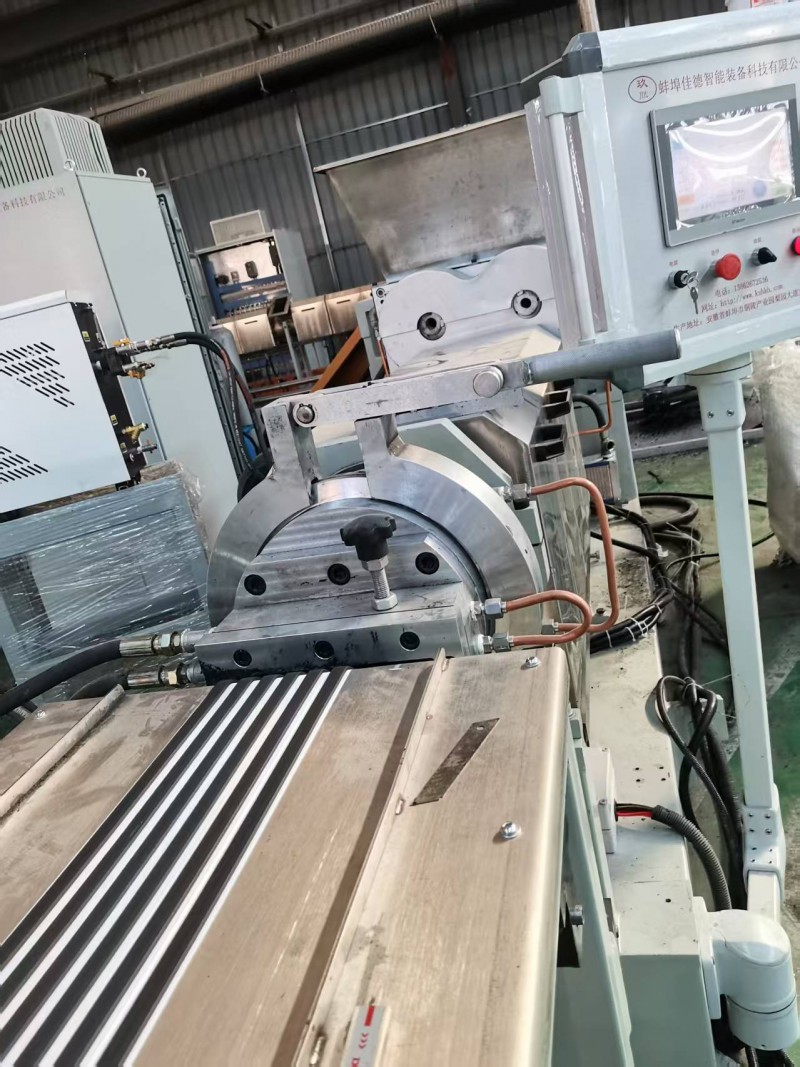
牵引与切割**
• **牵引机**:调节牵引速度与挤出速度同步,防止拉伸变形(牵引比1.05-1.10)。
• **切割方式**:
◦ **定长切割**:用于密封条、胶带(长度误差±1 mm)。
◦ **卷取**:用于胶膜、胶管等连续产品。
后处理与检验**
表面处理**
• **涂覆处理**:部分产品需喷涂离型剂或增粘层(如胶带背涂硅油)。
• **印刷标识**:通过喷码机标记批次、规格等信息。
性能检测**
包装与存储**
• **防粘包装**:胶条、胶膜用PE膜隔离,避免粘连。
• **环境要求**:存储温度10-30℃,湿度<60%,远离热源和化学品。
**环节** | **控制参数** | **允许误差** | **异常处理** |
|----------------|---------------------------|-----------------------|----------------------------|
| **塑化温度** | 机筒温度(150-200℃) | ±2℃ | 检查加热圈或温控模块 |
| **螺杆转速** | 20-60 rpm | ±5% | 调整喂料速度或检查电机负载 |
| **机头压力** | 15-30 MPa | ±3 MPa | 清理口模堵塞或降低喂料量 |
| **冷却水温** | 10-25℃ | ±3℃ | 调节冷却水流量或更换制冷系统 |
| **牵引速度** | 与挤出速度匹配(1:1.05-1.10) | ±2% | 校准牵引机编码器或调整变频器参数 |
常见问题与解决方案**
表面气泡或裂纹**
• **原因**:原料含水率高或塑化温度过高。
• **解决**:加强原料干燥(80℃烘4小时)、降低均化段温度5-10℃。
尺寸波动**
• **原因**:牵引速度与挤出速度不匹配或口模温度不均。
• **解决**:校准牵引机同步性、检查口模加热圈分布。
塑化不均**
• **原因**:螺杆压缩比过低或喂料不稳定。
• **解决**:更换高压缩比螺杆(2.5→3.5)、加装强制喂料器。
工艺优化方向**
节能降耗**:采用电磁加热替代电阻加热,能耗降低30%。
智能化控制**:通过传感器实时监测熔体压力、温度,AI算法动态优化工艺参数。
绿色生产**:集成废气收集系统(活性炭吸附+催化燃烧),VOC排放减少90%。
总结**
丁基胶挤出机的生产流程以**精准控温、稳定压力、速度匹配**为核心丁基胶挤出机价格_丁基胶挤出机价格,通过原料预处理、塑化挤出、冷却定型和后处理等步骤实现高效连续化生产。严格的质量控制和工艺优化可显著提升产品合格率(≥98%),降低综合成本(能耗减少15-20%),满足建筑、汽车、新能源等领域的高标准需求。
光伏丁基胶挤出机设备 http://www.bsjdl.com/sell/show.php?itemid=29919